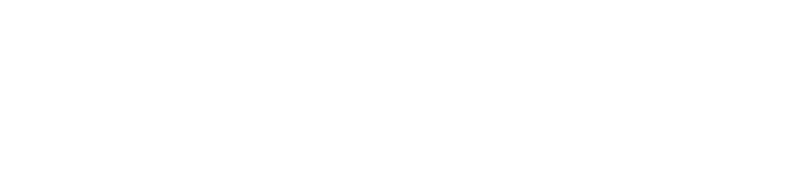
Improving Quality
to improve quality of life
Millions of lives are affected by drug shortages and recalls.
The burden is felt by the pharmaceutical industry, healthcare providers, and directly by patients. Most impacted:
- Emergency care – 87%
- Anesthesia care – 85%
- Pain management – 81%
- Infectious disease treatment – 71%
- Cardiovascular care – 68%
Most drugs in short supply are older, low margin, generics that compete for equipment occupancy time with more profitable medications.
Quality issues in the final production stages can quickly make production hard to financially justify for manufacturers working to address demand.
Over half of the medications in short supply are injectables that are freeze-dried to stabilize and preserve them in a process called lyophilization. Just before they are injected, the dried compounds or ‘cakes’ are reconstituted (typically) using a saline solution. The ‘cakes’ often do not dissolve readily, which can lead to problems.
Patients can suffer when care providers rush and inadvertently inject solids, or when delicate structures are damaged by vigorous shaking to hurry reconstitution. The effects: painful injections, or harm from a less potent medication.
Long reconstitution times disrupt care providers, who also have no way to detect if the potency of a drug or vaccine was damaged as it was reconstituted. The effects: delays, and potential harm due to ineffectual treatment.
Pharmaceutical manufacturers are burdened with lyophilization processes that are slow, expensive, and labor intensive. To make matters worse, conventional lyo has a high incidence of waste due to human error and contamination. To combat errors, operators use conservative/longer cycle times: often 3 to 4.5 days. The effects: lyophilization becomes the costly bottleneck, and manufacturers have to make difficult choices.
Currently, none of the stakeholders win.
Our goal is to increase patient availability of vital injectable drugs.
To make this happen we’re working on a new approach to freeze-dry pharmaceuticals and vaccines. It has the potential to provide pharmaceutical manufacturers a lyo process that is consistent, efficient, and cost effective. We plan to tell you more about it soon.